Searching for new ways to build sustainable homes, Earl Forlales decided to look not into the future, but to the past.
His grandparents, like generations of Filipinos, lived in a “Bahay Kubo” — a traditional, boxy, single-story bamboo hut on stilts, indigenous to the Philippines. “Filipinos have been using bamboo (for housing) even before colonial times, for thousands of years,” he says.
Strong and flexible, bamboo is one of the fastest-growing plants in the world: while soft and hard woods can take between 40 and 150 years to mature, bamboo is ready to harvest in as little as three years. When treated and engineered, it can last for decades. Realizing the Bahay Kubo could be adapted to create a contemporary home, Forlales began designing his own bamboo houses.
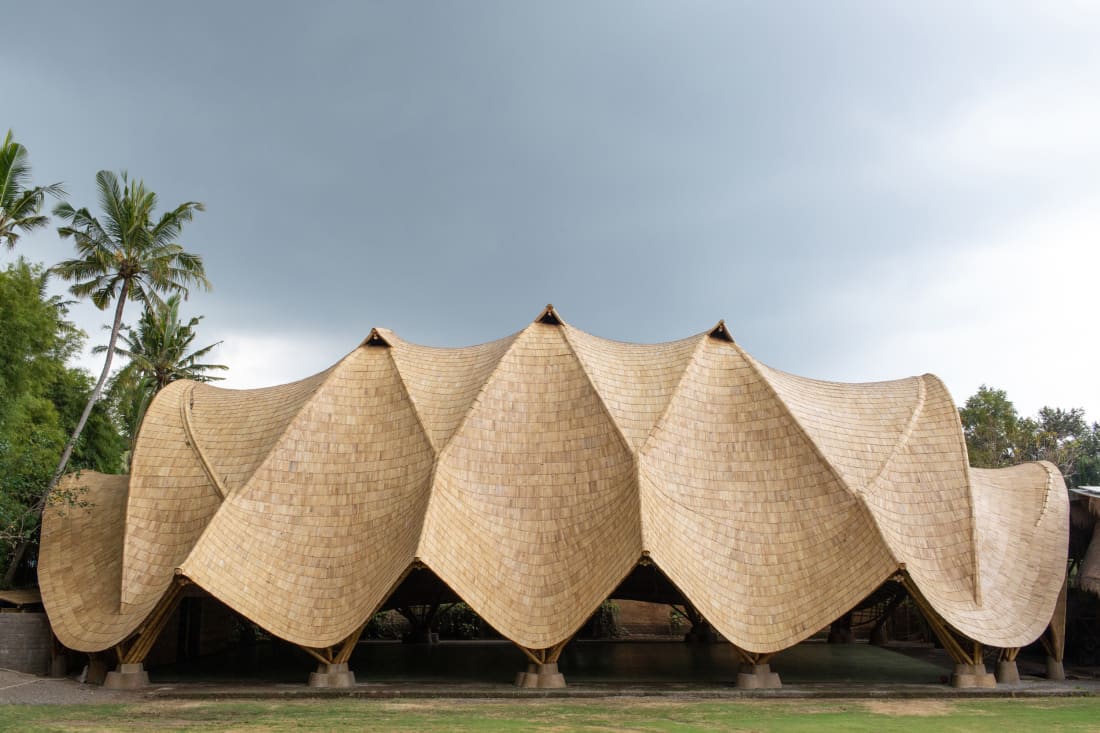
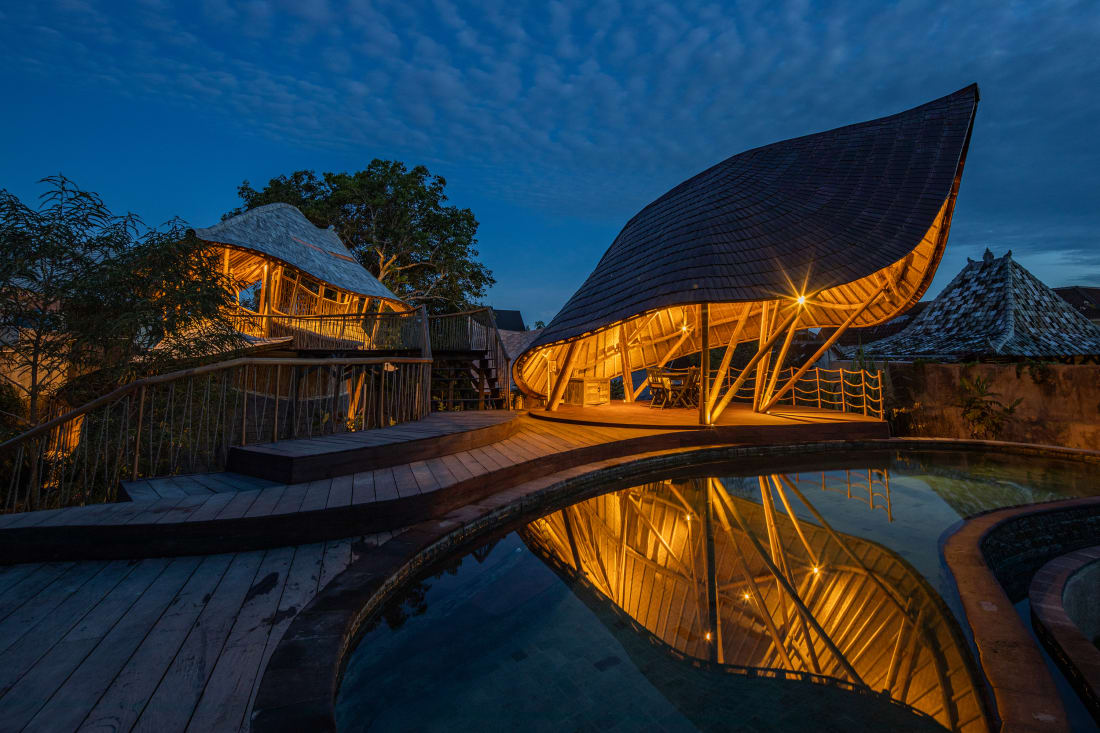
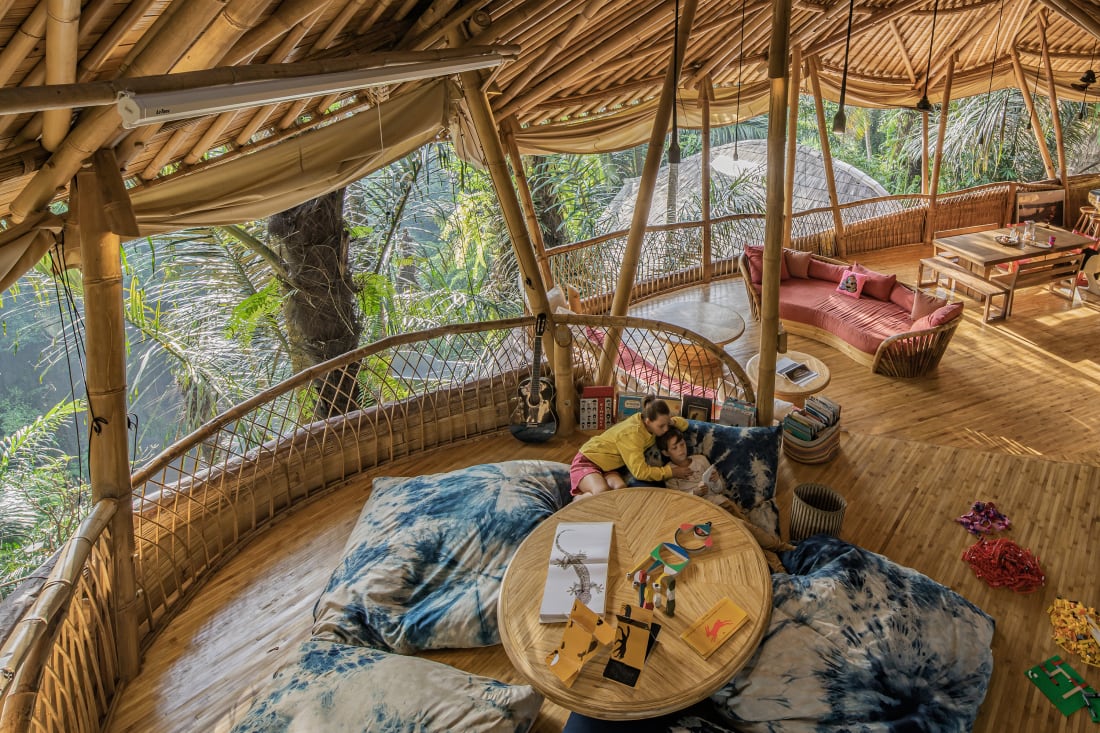
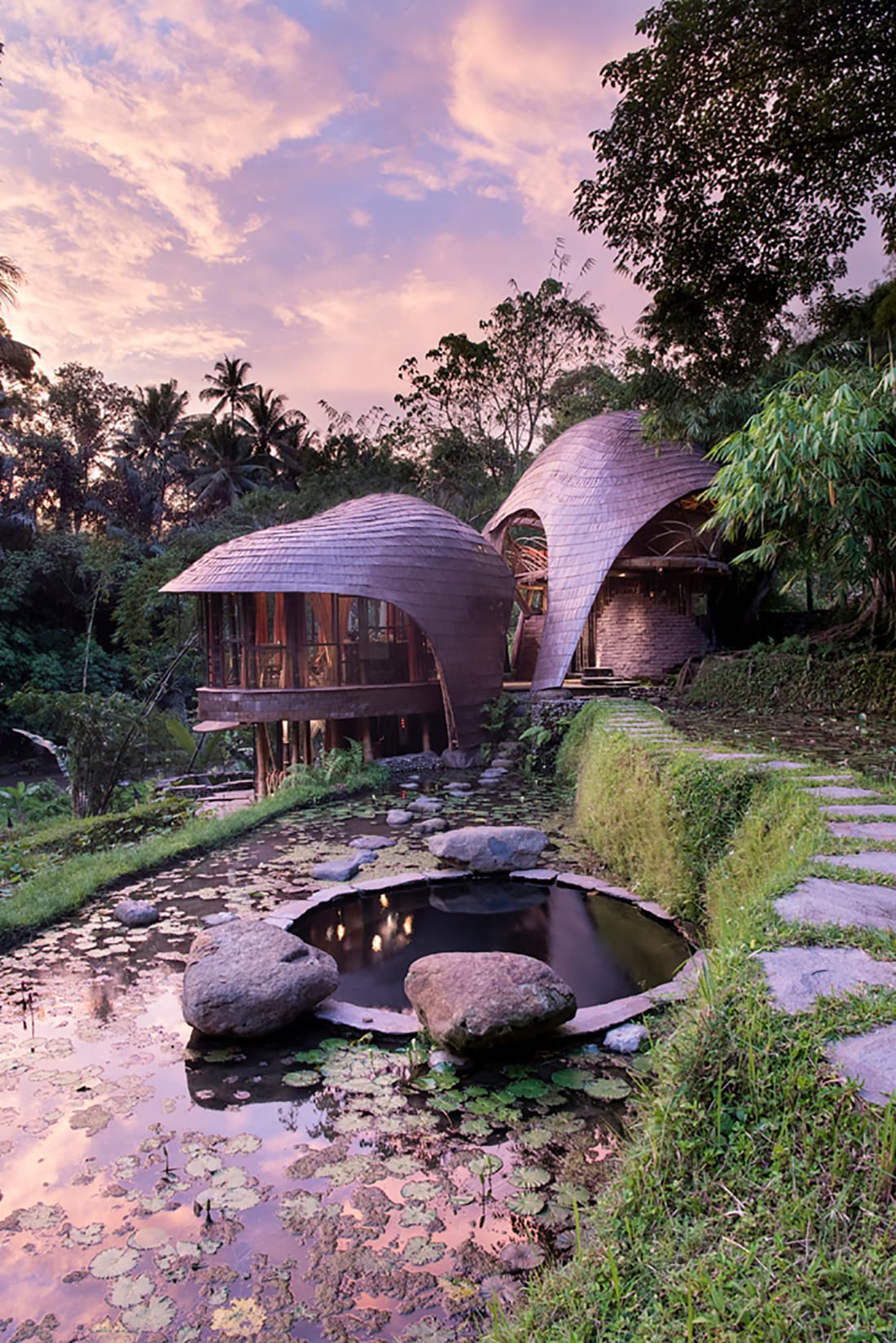
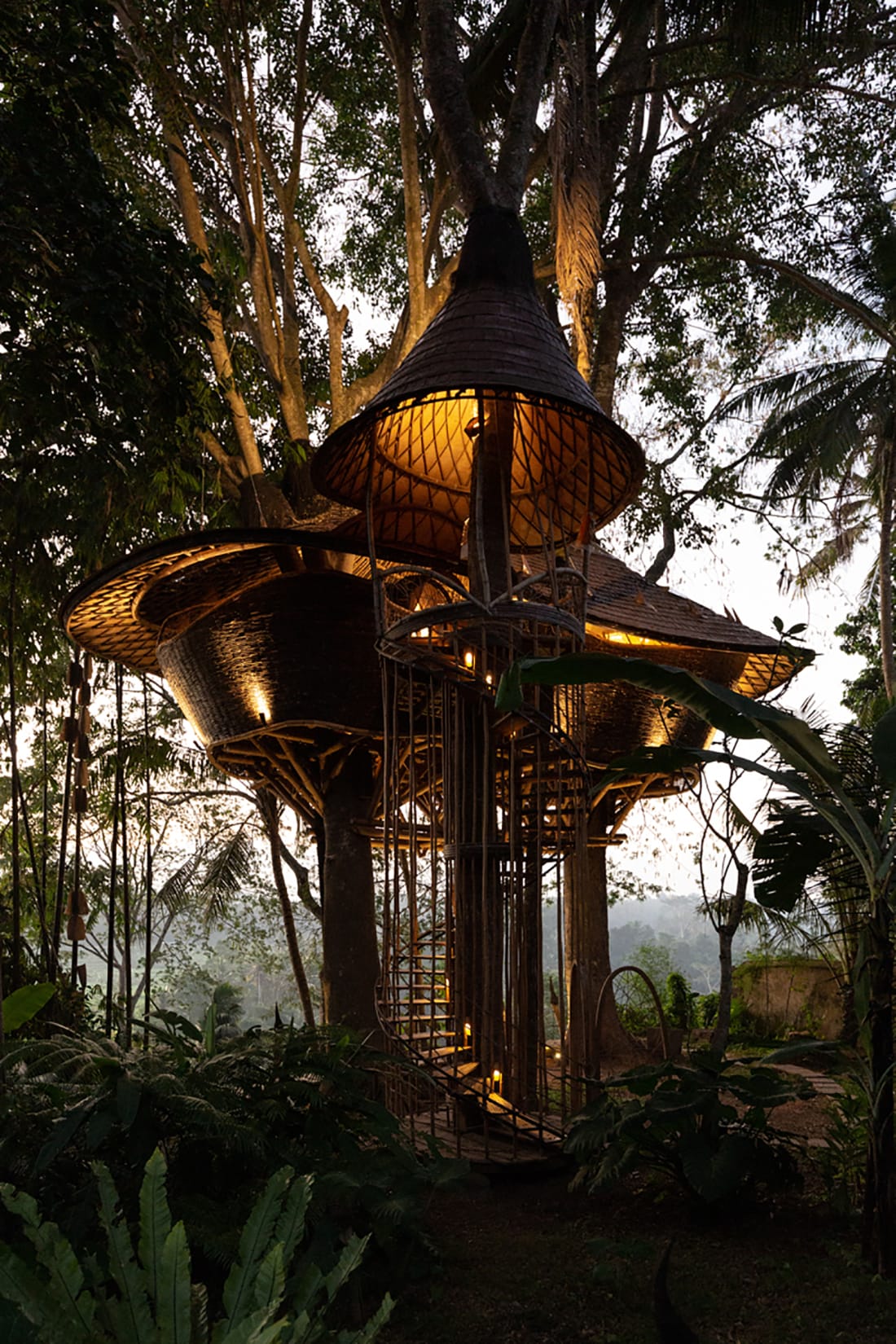
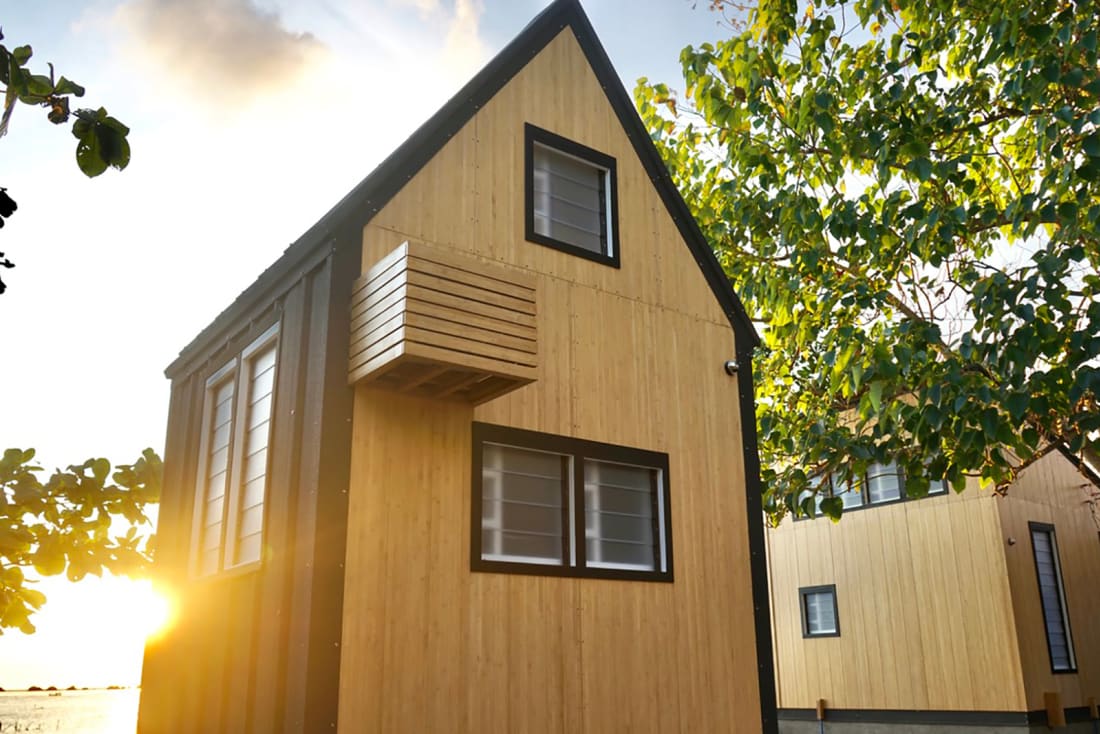
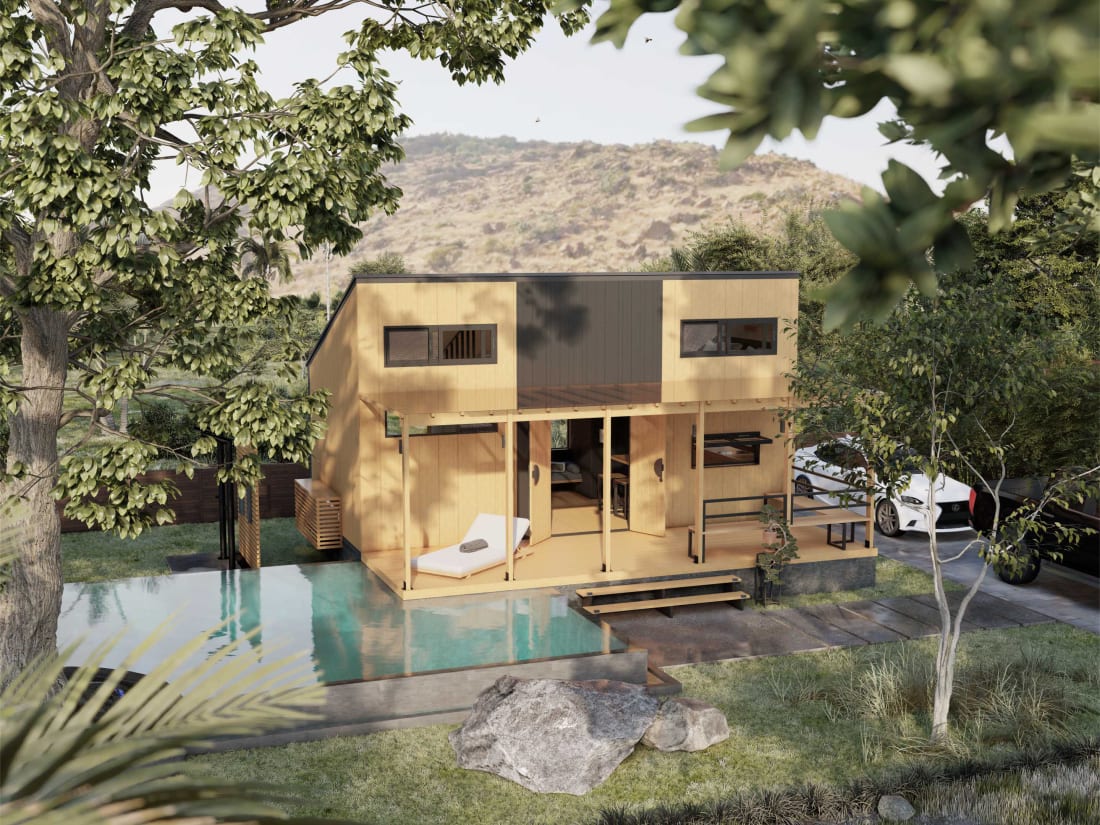
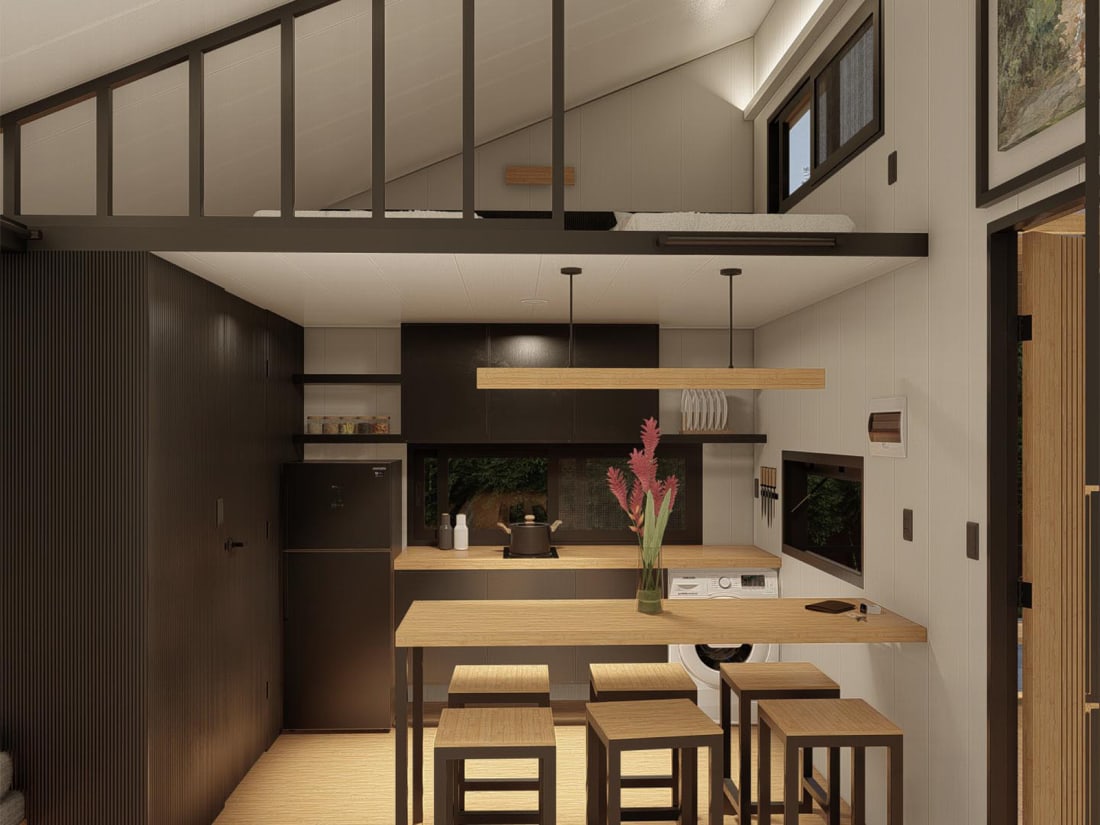
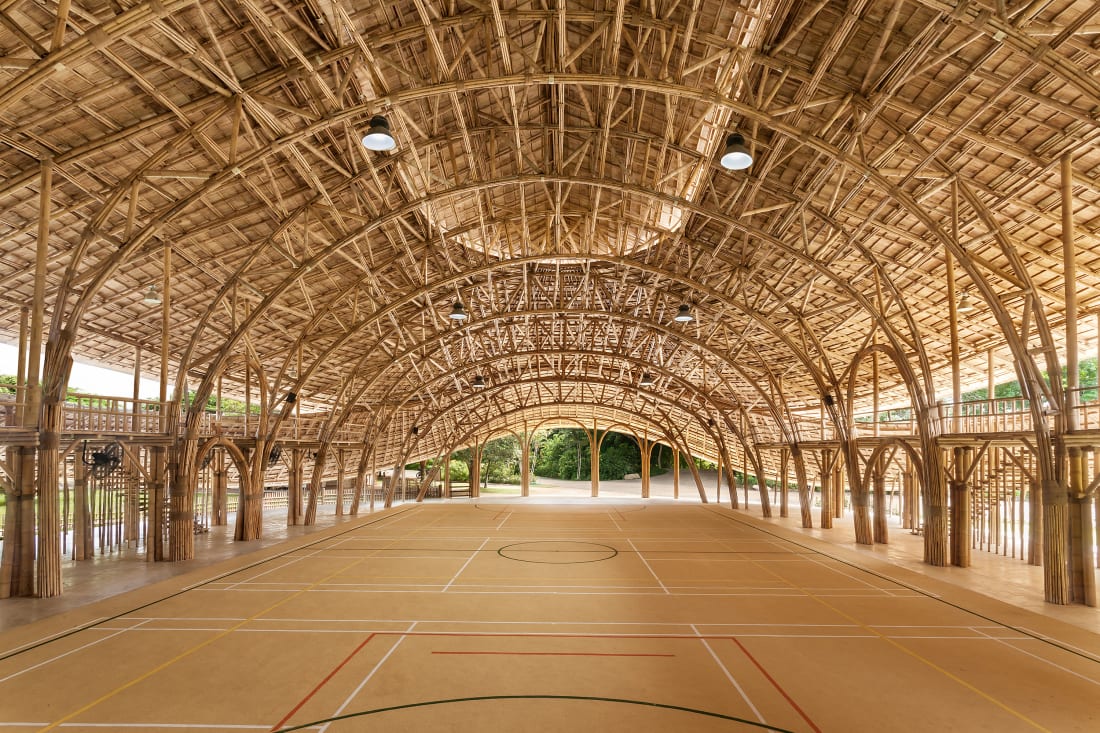
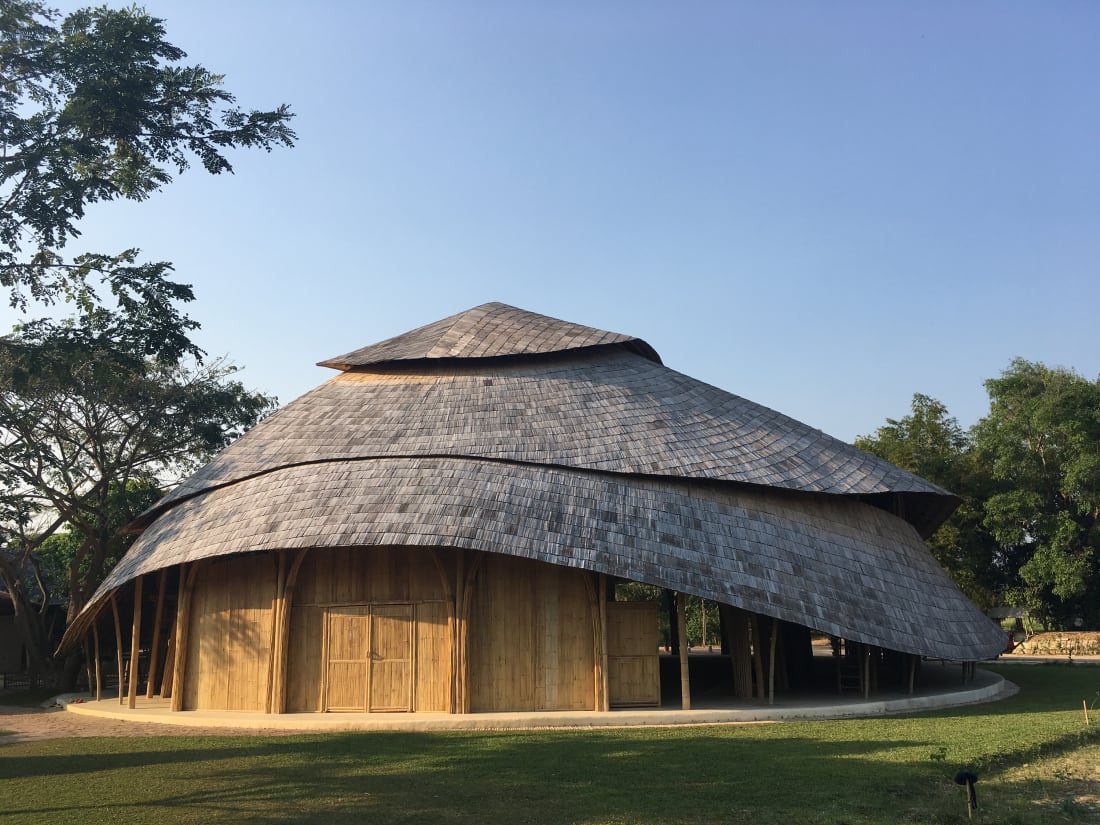
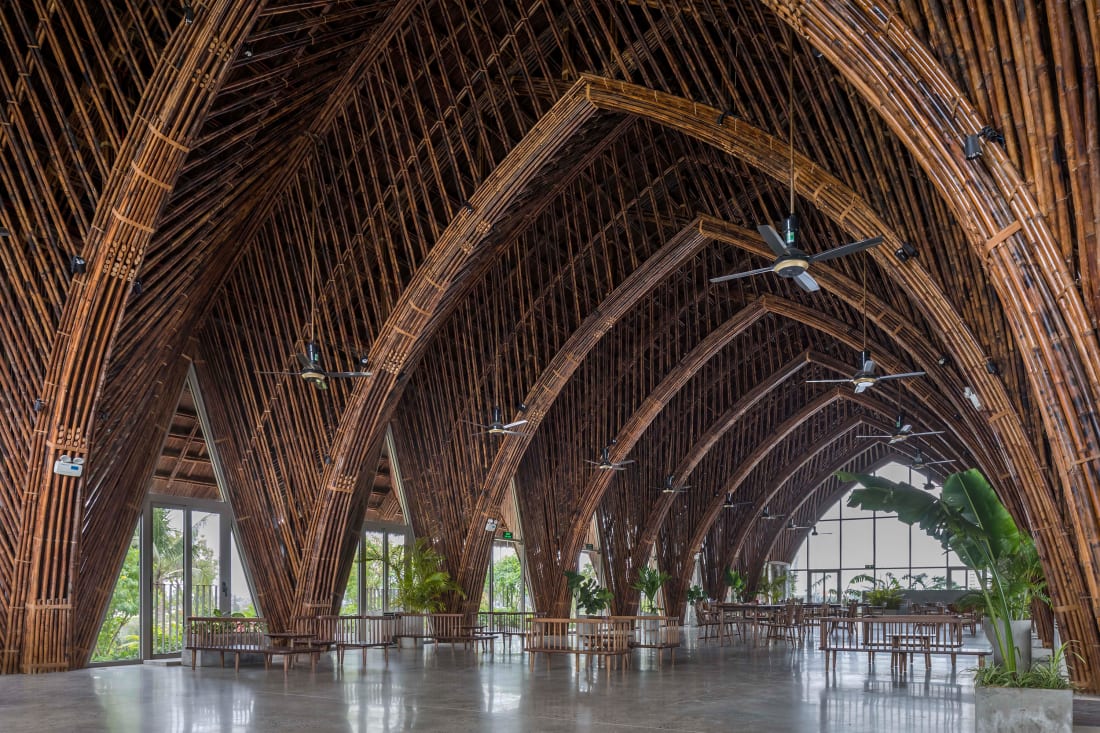
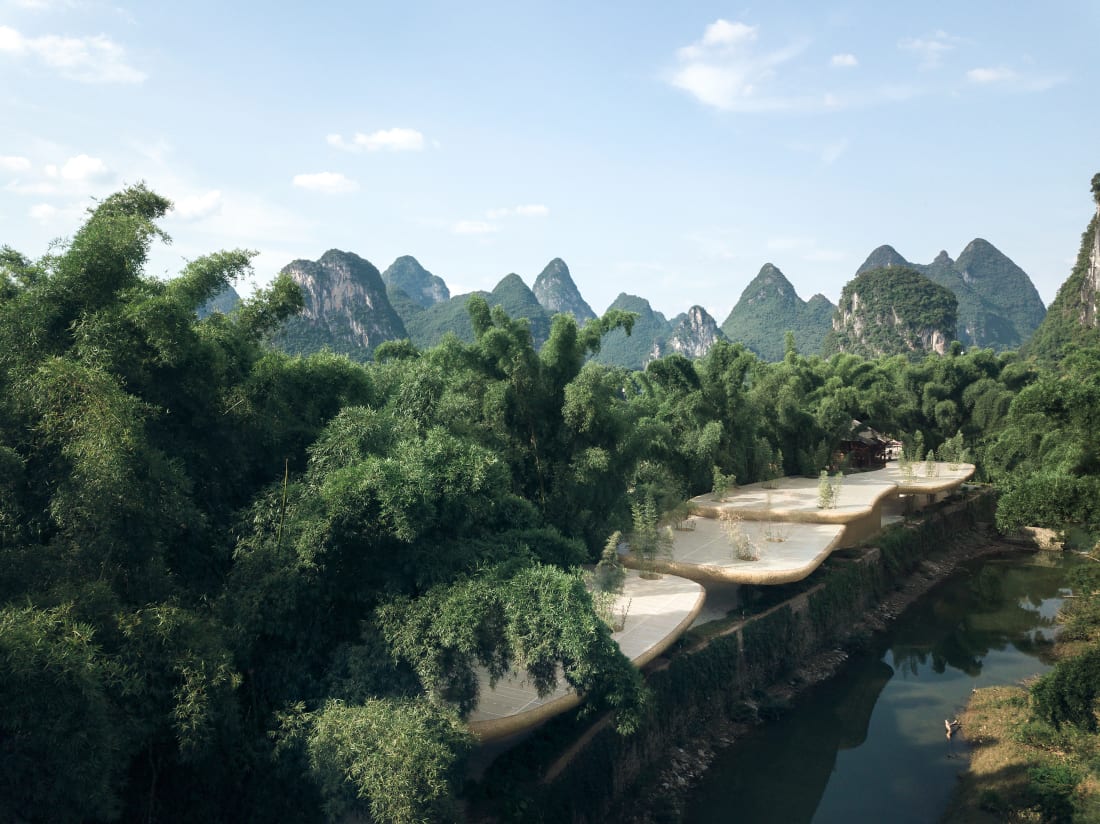
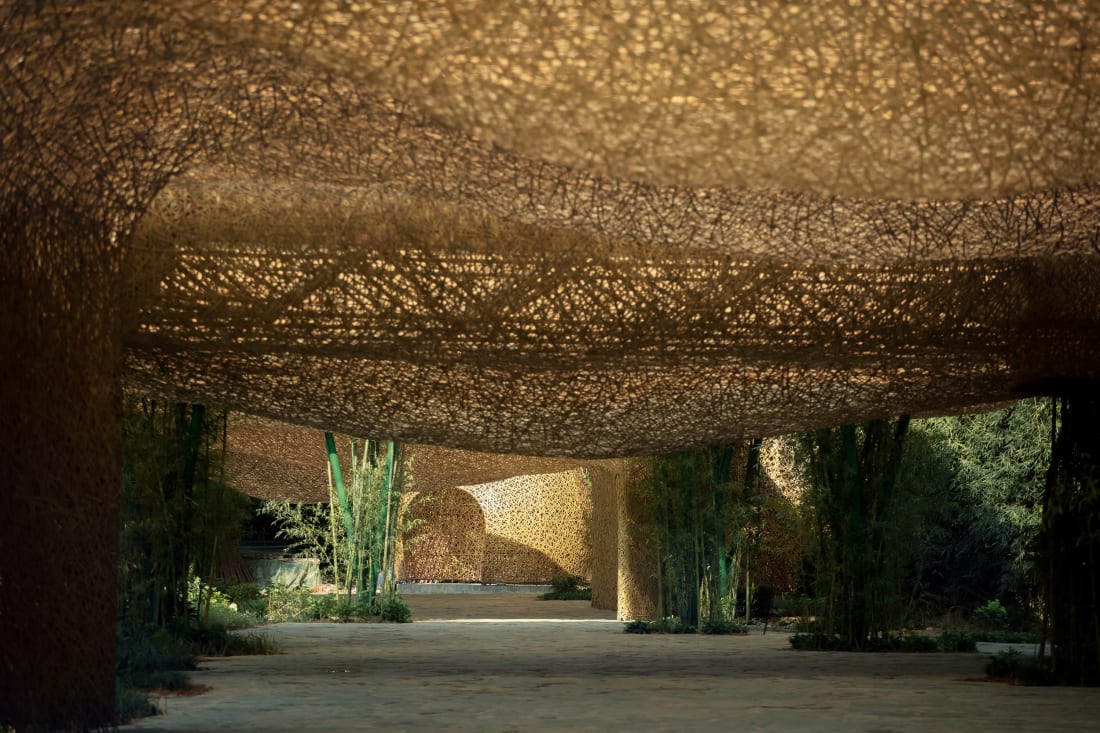
After winning the “Cities for our Future” challenge run by the UK’s Royal Institution of Chartered Surveyors in 2018, the materials engineering graduate turned his idea into a company, co-founding Cubo in 2019.
The company launched production of its prefabricated homes in November 2020. The structures can be assembled in just a few days and are predicted to last up to 50 years, says Forlales. He hopes that Cubo’s modular designs and use of bamboo can “help accelerate sustainable building” while also providing affordable housing solutions for the Philippines’ housing crisis.
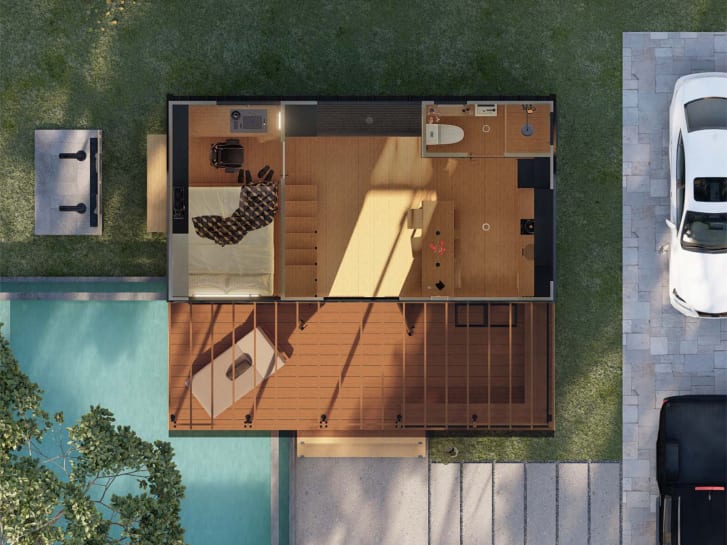
The zero-waste ‘Greenhouse’ is providing a blueprint for future homes
Cubo’s bamboo homes incorporate many aspects of the traditional “Bahay Kubo” including a raised foundation and louvers, a type of window blind that allows natural ventilation and light.
But Cubo has given the bamboo hut a 21st-century upgrade, including modern light fittings and impact-proof polycarbonate windows. The Philippines is prone to earthquakes and typhoons, so the homes have been designed with natural disasters in mind. Metal “typhoon ties” are used as connectors between the walls, roof and floor panels, and the homes are further reinforced with poured concrete foundations, which replace the traditional stilts. While this gives the structures a solid base, concrete contributes to climate change. Forlales says the company is “exploring alternative foundation systems to further make our offering more sustainable” but this is still in the research stage.
The company’s first project was tested very quickly — in December 2020, just days after the first two homes were constructed, the region was hit by a magnitude six earthquake. Cubo’s houses survived unscathed.
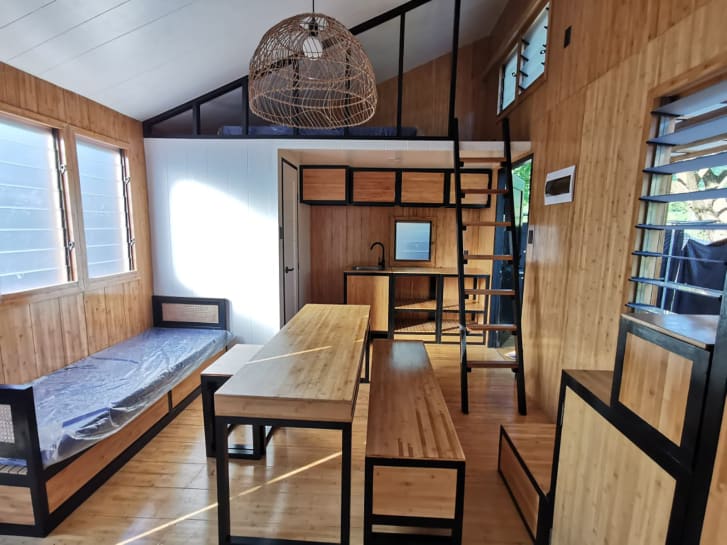
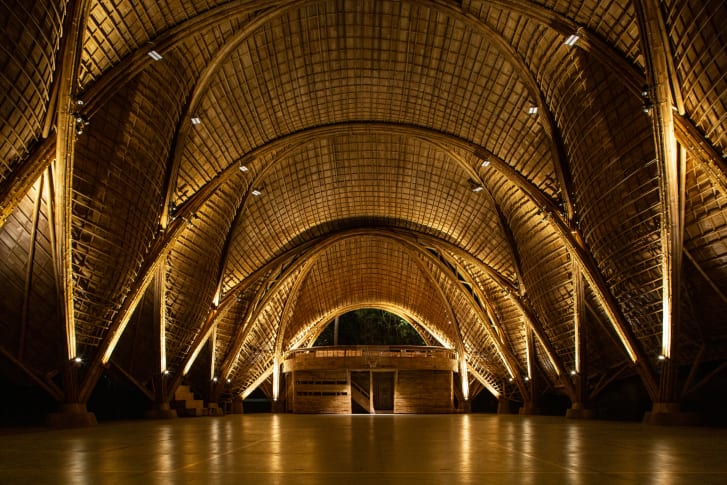
Ibuku specializes in sculptural villas, hotel resorts, and “green” school campuses made from bamboo. The Arc is an educational building at Green School Bali. Credit: Tommaso Riva/IBUKU
Engineered bamboo entered mainstream construction in the late 20th century, according to Bhavna Sharma, assistant professor of architecture at the University of Southern California and a member of the task force developing international standards for bamboo construction materials.
“Standards for mechanical testing of engineered bamboo materials are currently being developed; however, areas such as fire performance require extensive study,” says Sharma.
As a strong, fast-growing, and renewable material, bamboo could supplement sustainably harvested hardwoods, says Sharma, with the added benefit of bamboo plantations helping to restore degraded soil and land.
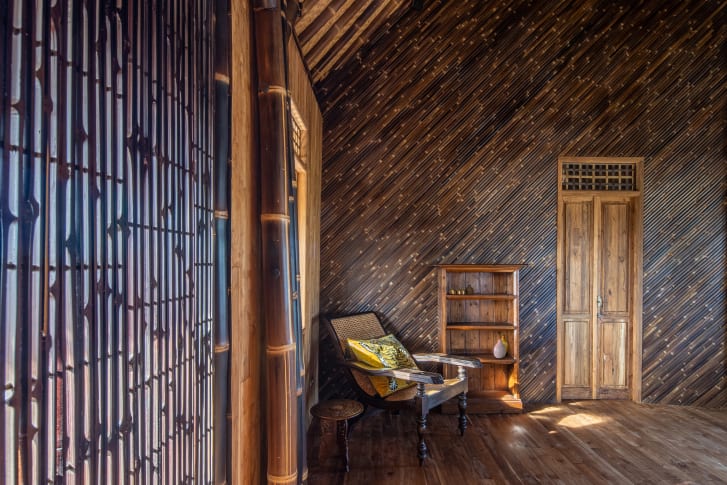
From the exterior structure to interior furnishings, Ibuku shows that bamboo can have varied applications in architecture and design. Credit: Indra Wiras/IBUKU
Helping out a housing crisis
While sustainability is bamboo’s primary advantage, it’s not the only reason Cubo is looking to the fast-growing grass as an alternative building material.
The Philippines is currently facing a severe housing shortage, with an estimated 4.5 million people living homeless in 2021, and a deficit of affordable homes.
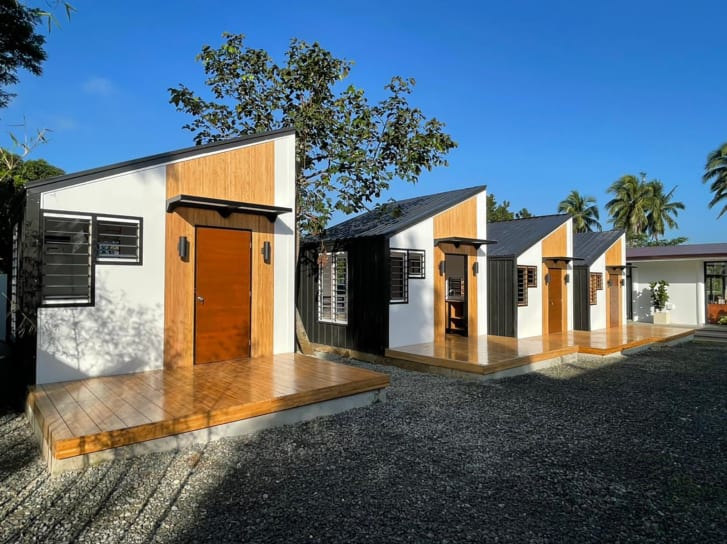